SHERIDAN – In the spring of 2021, Sheridan Memorial Hospital’s attempts to reduce patient falls centered around reactive solutions to an issue that plagues health care facilities across the country.
After working through a more than yearlong process to reduce falls and increase patient safety, staff across the organization shifted their mindsets. They began focusing on evaluating processes as the means to reduce falls. As a result, the culture within the hospital has become one of continuous improvement and the proactive actions of staff have reduced falls by approximately 15 percent from 2022 to 2023.
This success story from SMH represents just one example of teams working to address concerns across the healthcare organization. Some of the work takes place within one unit, while other projects cross departments and involve many stakeholders.
The creation and utilization of Lean management tools at Sheridan Memorial Hospital served as the mechanism by which teams could work through large, systemic problems without becoming overwhelmed, deterred or delayed. But, the implementation of Lean practices didn’t take place overnight.
Why Lean?
The idea of Lean management focuses on increasing quality and efficiency by decreasing wasted resources like time, money or effort. Lean emphasizes constant experimentation as a way of creating a culture of continuous improvement.
Recognizing the positive effects a Lean management system could have at Sheridan Memorial Hospital, the SMH Board of Trustees approved an initial three-year contract with Simpler Consulting in 2018.
Simpler was founded in 1996 on the basic premise that the principles, tools and techniques of Lean apply anywhere work is done. In workshops led by Simpler, Sheridan Memorial Hospital launched a coaching program to help key players within the organization build the necessary skills to move the Lean transformation forward.
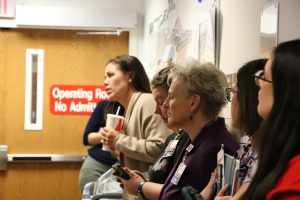
Sheridan Memorial Hospital team members involved with the Women’s Health Unit value stream discuss ongoing projects Tuesday, April 2, 2024.
Then, those newly trained leaders began working with teams within the hospital to introduce and teach the Lean system. Early experiments with the management system began in areas such as Internal Medicine and Revenue Cycle.
Approximately one year into the transformation, SMH rolled out the Management for Daily Improvement (MDI) system, a framework that facilitates strategy deployment and engagement with all employees throughout the organization.
While the work being done to make improvements and better the patient experience was well-intentioned, the organizational structures needed further refinement.
“People would go into rapid improvement events and take on big projects, work on them for a week and come out of it with great ideas, but struggled to implement standard work because there was no structure in which to do it,” said Brittany Goodvin, Lean manager.
As a result, the Lean team was tasked with implementing huddles across the organization as a means to implement standard work. The team worked with leaders to outline what huddles would look like. Pilot huddles took place in the Emergency Department and laboratory as well as on the medical/surgical unit. Then the organization began to build on what was learned from those experiments.
“What we needed was 800 problem-solvers,” Goodvin said. “With 800 people working through issues around quality, safety and patient experience, we could get where we’re trying to go.”
As the Lean team and organizational leaders continued developing the Lean infrastructure within SMH, they identified gaps and added tools such as one-on-ones and leader standard work to the team’s repertoire. They learned that in order for Lean to work, SMH needed people to own the goals of the organization, break them down and utilize the proper teams to address them.
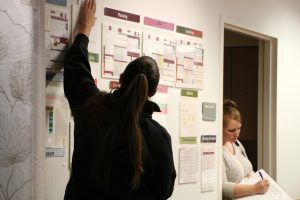
Kim George, Women’s Health Unit manager, talks through her team’s continuous improvement work while Lean Transformation Facilitator Collette Miller makes note of countermeasures and action items on Tuesday, April 2, 2024.
Real-time Lean management
When the COVID-19 pandemic began in the spring of 2020, the hospital faced unprecedented challenges. Among them, SMH needed to quickly set up testing and vaccination centers.
This represented an opportunity to not only talk about Lean management systems but use them to move big projects forward quickly. The team utilized Lean management tools to develop and deploy standard work for testing and vaccination centers. Visual management was used to quickly help remind staff of what needed to be done. Tiered huddles allowed for information and barriers to be escalated to appropriate leadership levels, including to chiefs and directors, who during the pandemic comprised an incident command team. That incident command team then became a Tier III within the huddle system and remains in place today.
COVID preparation and management left little other time for improvement work, so instead Lean efforts focused on showing how management tools could be used, then training other managers and leaders to use them.
As the urgency of the pandemic waned, teams returned to value-stream conversations and Lean projects, representing a turning point in the health care system’s Lean journey.
By this point, teams within the hospital had been utilizing daily huddles for months, the tiered huddles had been put into place and directors had begun to embrace the utilization of leader standard work and guiding principles.
“We now have leaders at all levels who embrace the Lean management system and who have the capability and capacity to lead Lean across the organization,” said Mike McCafferty, Sheridan Memorial Hospital CEO.
Achieving results
Over the last year, departments across Sheridan Memorial Hospital have started utilizing Lean tools more effectively. From daily huddles and other MDI to leader standard work, swarms and rapid improvement events — individuals and teams have embraced the use of critical thinking to address problems and achieve continuous improvement.
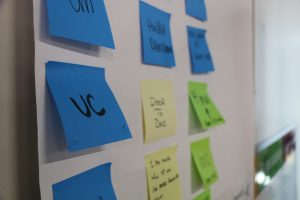
Sticky notes track some of the work being done within the Lean management system by departments at Sheridan Memorial Hospital. The continuous improvement work is reviewed on a regular cadence by hospital staff.
Deployment of critical strategic goals across departments in 2023 meant each department had a metric for which to aim. As the first iteration of projects wrap up, Sheridan Memorial Hospital staff have much to show for their efforts. The nursing staff on the medical/surgical unit decreased falls by 30 percent. The teams in the Women’s Health Unit created new standard work that allows for women to stay with their newborn and support person following cesarean sections. Big Horn Surgical created new discharge policies and workflows to increase patient education. Urgent Care cut its average “door to doc” time in half, from about 30 minutes to approximately 15 minutes.
While generating buy-in from staff took time, showing that the processes work has built additional capacity.
In the Emergency Department, as an early project the team redesigned its triage process to be more functional for patients and staff. Dr. Luke Goddard said he was initially skeptical of the Lean management system but said through the triage project he saw how processes could be improved for both patients and staff.
“I think over time many people have had similar experiences to what I described above and now have more appreciation for Lean processes and tools to improve their work,” Goddard said.
The managers and staff who have seen these projects through have celebrated and credited the Lean management system with their success. For example, the Women’s Health team said they had wanted to complete the project around recovering cesarean sections for years, but until implementing Lean, didn’t have the tools to do so effectively.
Milestone of transformation
As the hospital continues to grow and adapt to the community’s needs, new projects will require all staff to continue embracing the Lean management system, MDI tools and continuous improvement mindset.
As part of the “Growing for You” campaign, Sheridan Memorial Hospital will develop a facility to provide mental health services — particularly a crisis stabilization center — by the end of 2026. Goodvin, who has led the Lean department, will transition into the role of Director of Behavioral Health.
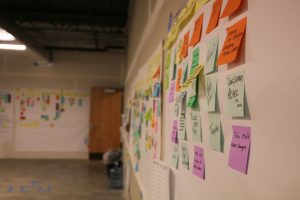
Teams meet regularly to track projects and ensure all of the necessary people are involved in continuous improvement projects at Sheridan Memorial Hospital.
Just as safety and quality stretch beyond a single department — integrated into every aspect of the organization — the Lean management system will continue to move Sheridan Memorial Hospital forward by living where any work is done.
“We will continue to develop Lean leaders at all levels of the organization,” McCafferty said. “I expect that our managers and directors will build expert knowledge of Lean management as a general requirement of their work. Just as important is the leadership capacity we are building across the entire health system. Staff at all levels — including physicians and clinical care staff, accountants, environmental services staff and administrative staff — are working every day to improve the work they do that aligns with our organization’s strategic priorities.”
A Lean facilitator will remain with the organization, under the umbrella of Tommi Ritterbusch, director of continuous improvement.
“This is a really exciting sign,” Goodvin said. “It shows the maturity and growth of the organization. This is what should happen; it’s a testament to all of the leadership and the commitment to develop problem-solvers throughout the organization.”
Successes, particularly over the last six to 12 months, have shown what Sheridan Memorial Hospital staff are capable of achieving when utilizing the Lean management system. Now, with more than 800 people adopting Lean thinking and working together, continuous improvement has become and will continue to be part of the SMH culture.